Ceramic Flower Crafting Process
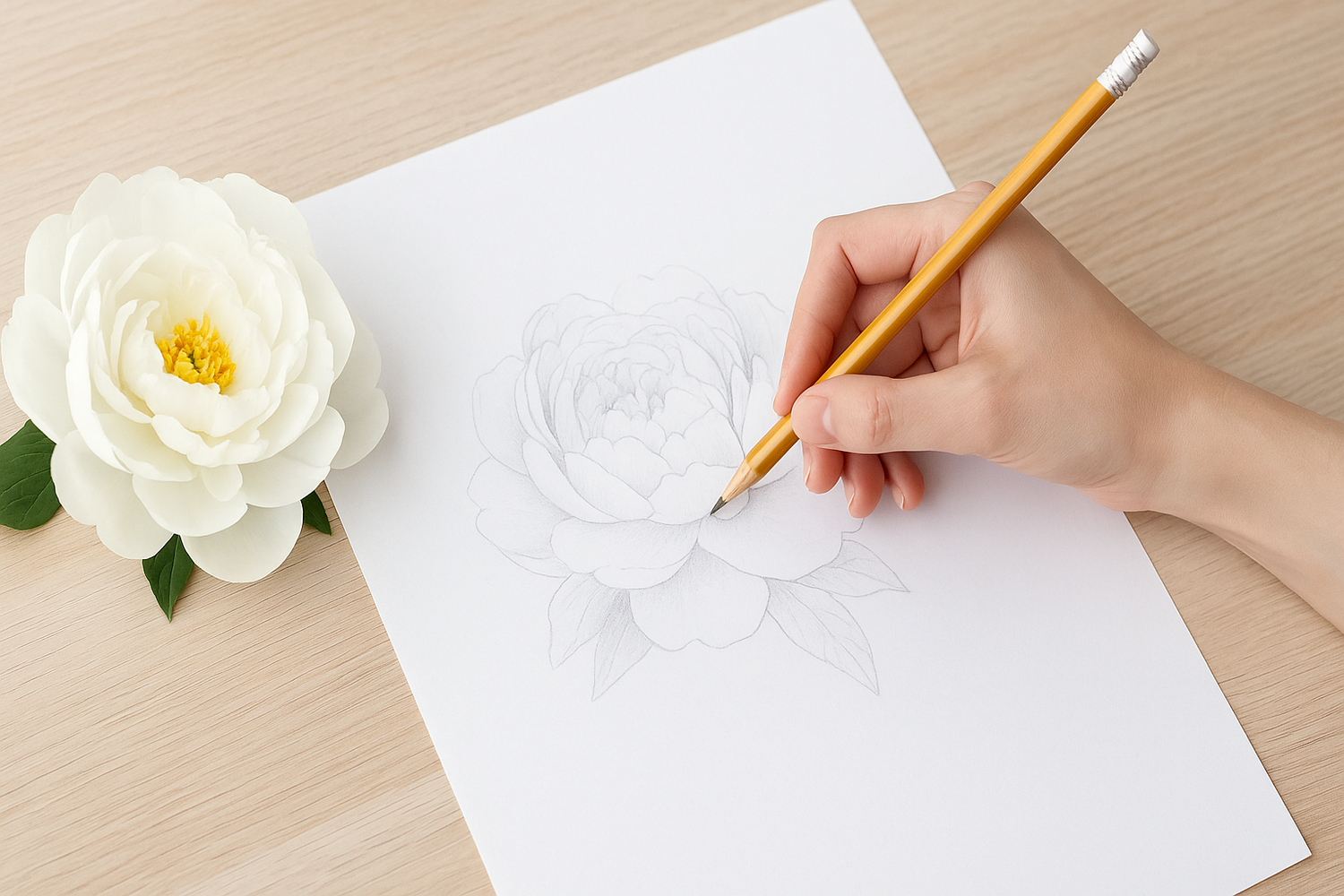
1:Conceptualization & Design
- election:
Determine flower species; observe real flower structures (petals, leaves, stamens, stems).
- Theme:
Define artistic theme (blooming, budding, withering, etc.).
- Composition:
Plan overall form, flower arrangement, and branch structure.
- Sketch/Model:
Create sketches or clay models for prototyping.
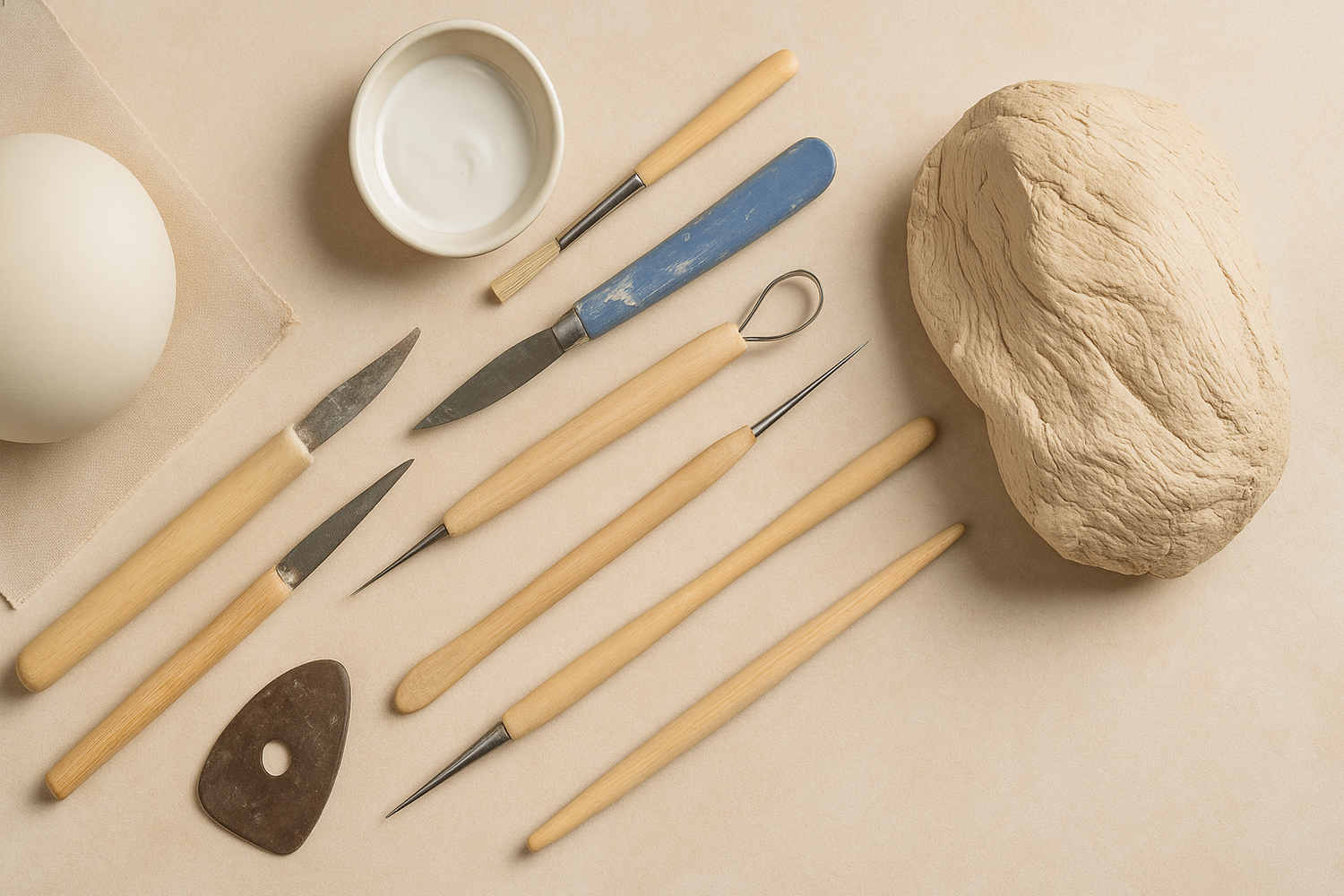
2:Material Preparation
- Porcelain Clay:
Select kaolin ("Guanyin Clay"), processed by washing, settling, and aging.
- Glaze:
Prepare "Jade White Glaze" (transparent).
- Tools:
Bamboo knives, carving tools, shaping sticks, molds, needles, brushes, etc.
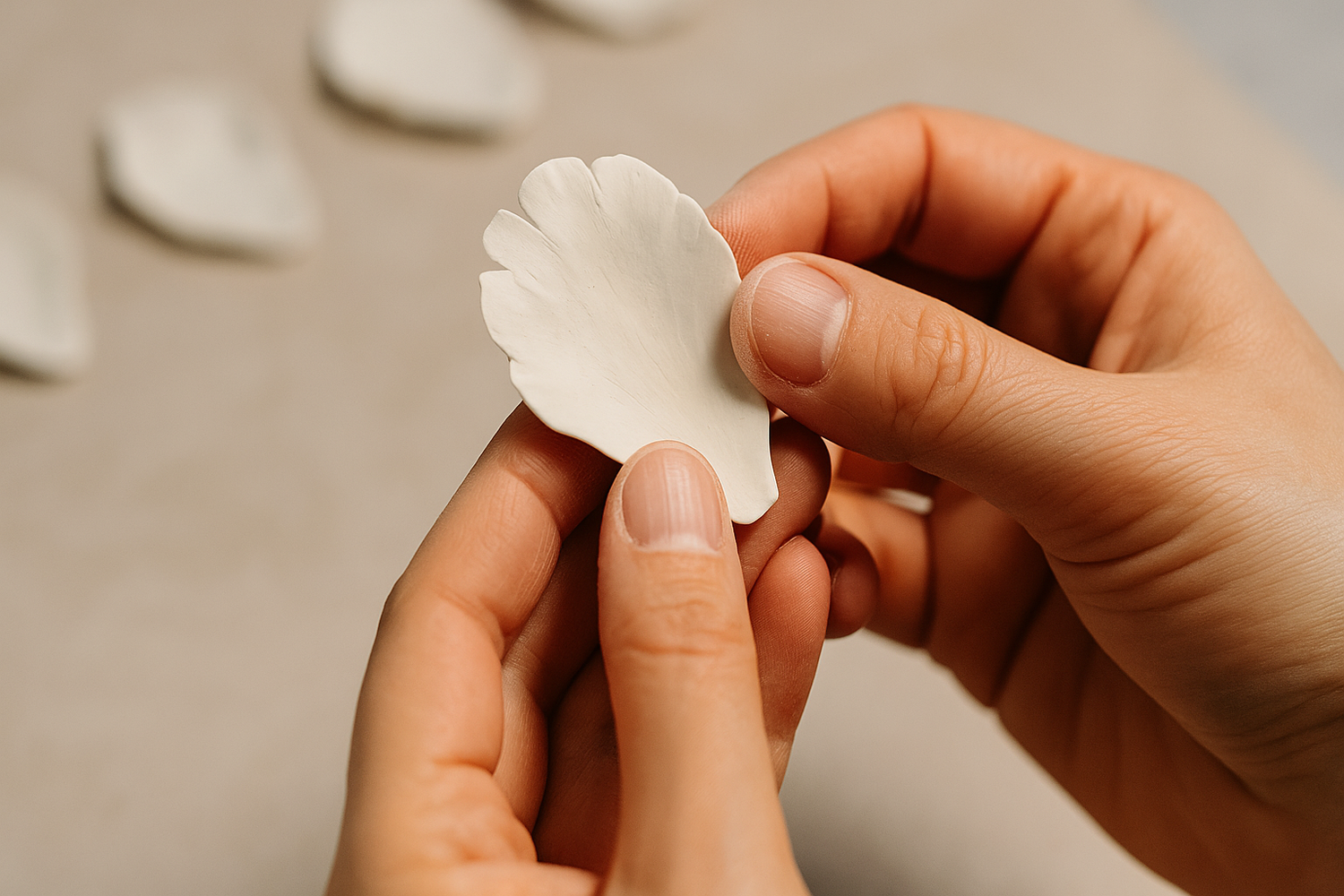
3. Shaping (Core Process)
- Petals: Roll clay into ultra-thin sheets (0.1-0.3 mm) → Cut contours → hand-carve veins → Shape curves → Air-dry to leather-hard state.
- Stamens: Twist clay into filaments/beads; dot glaze for pollen effect.
- Leaves: Same as petals; imprint leaf veins.
- Stems: Roll clay strips → Carve bark texture → Insert wire armature (anti-deformation).
- Assembly: Assemble with dilute clay slurry → Layer petals from center outward → Attach leaves/stems → Support with clay props.
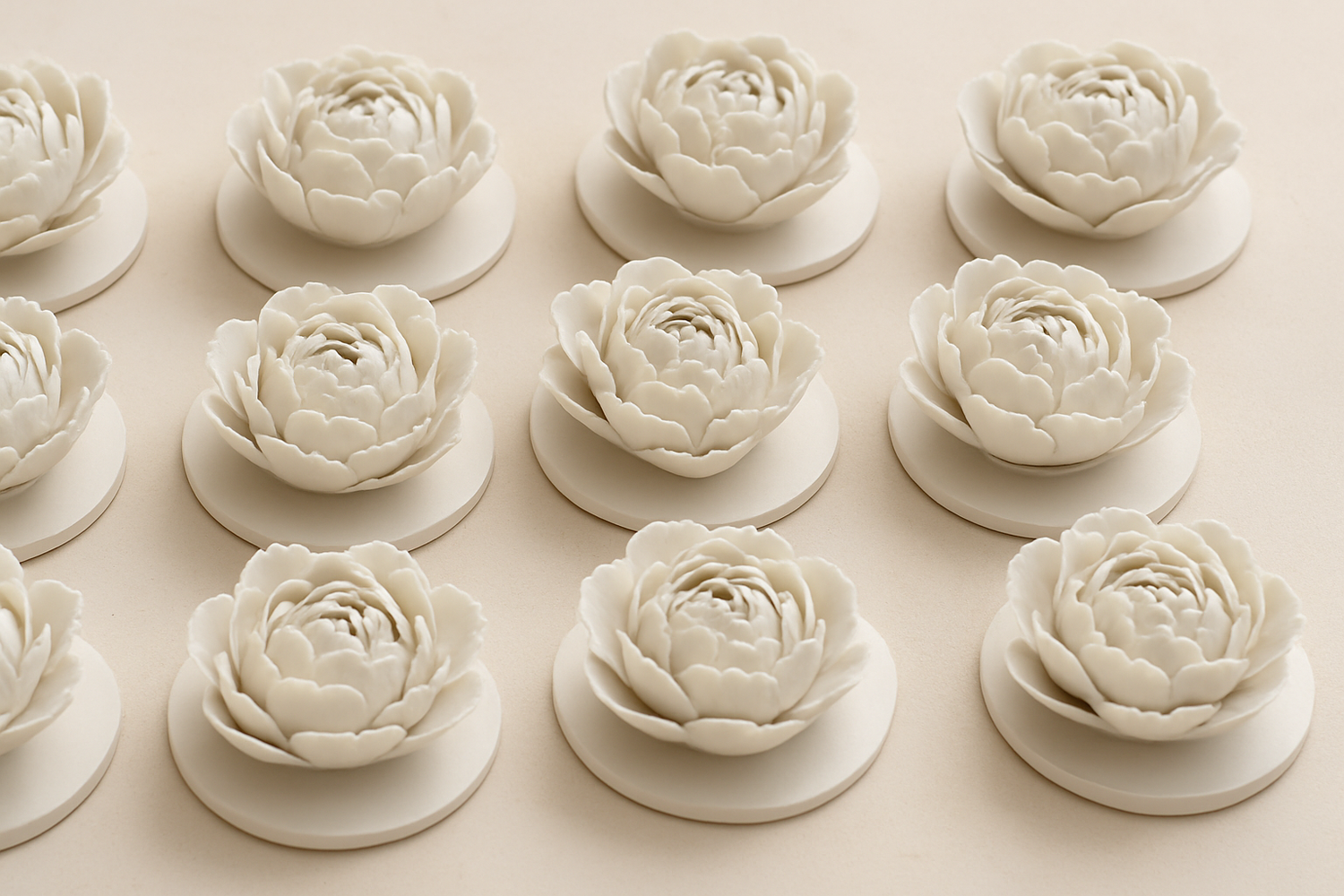
4. Refinement & Drying
- Detailing:
Smooth joints
→ Deepen textures
→ Adjust forms.
- Drying:
Air-dry for 7-30 days (shaded, ventilated, crack prevention).
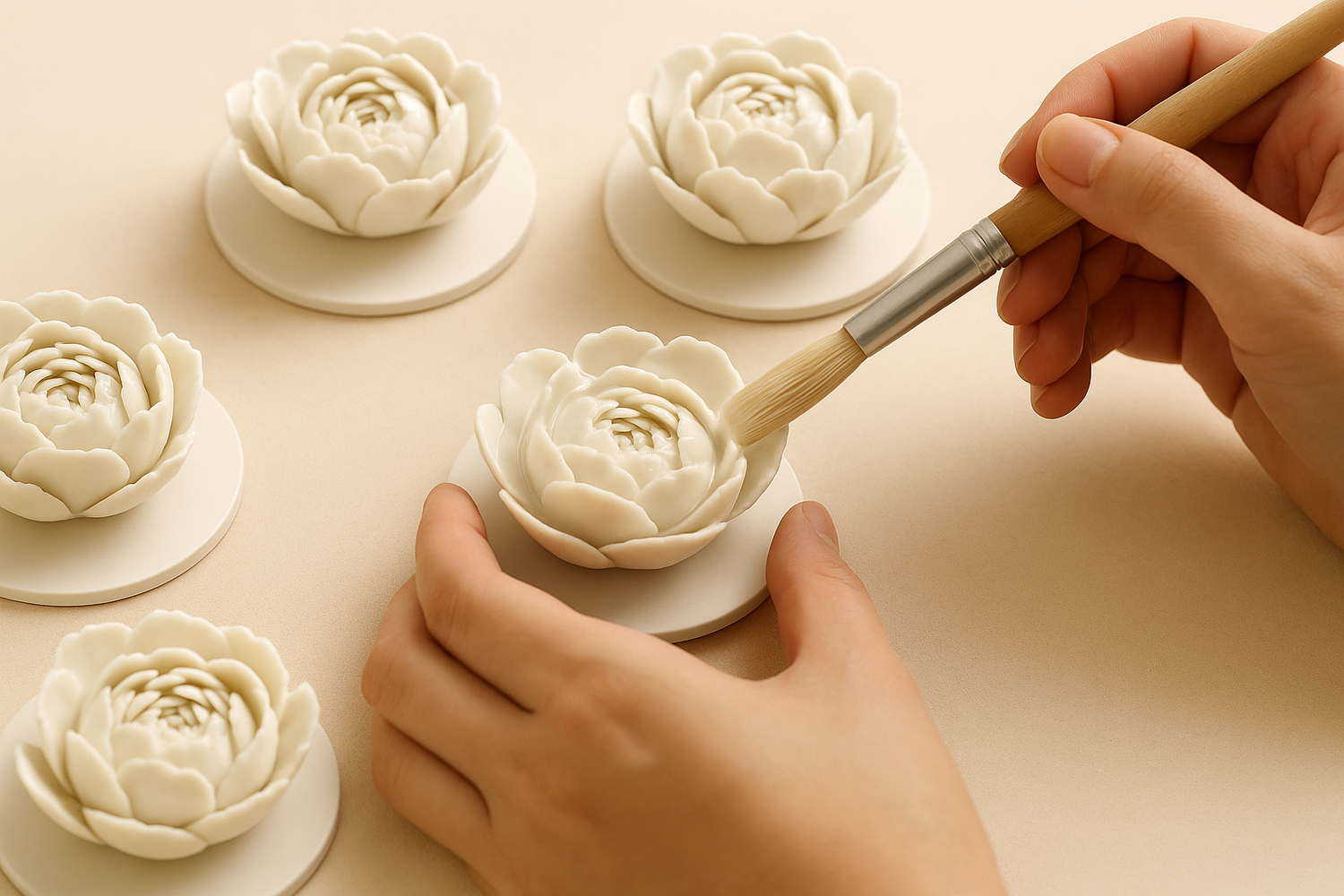
5. Glazing
- Cleaning:
Remove dust with soft brush.
- Application:
- Dip-glazing: For simple structures.
- Spray-glazing: (Primary method) For intricate details.
- Brush-glazing: For touch-ups.
- Foot Trimming: Scrape glaze off base to prevent kiln adhesion.
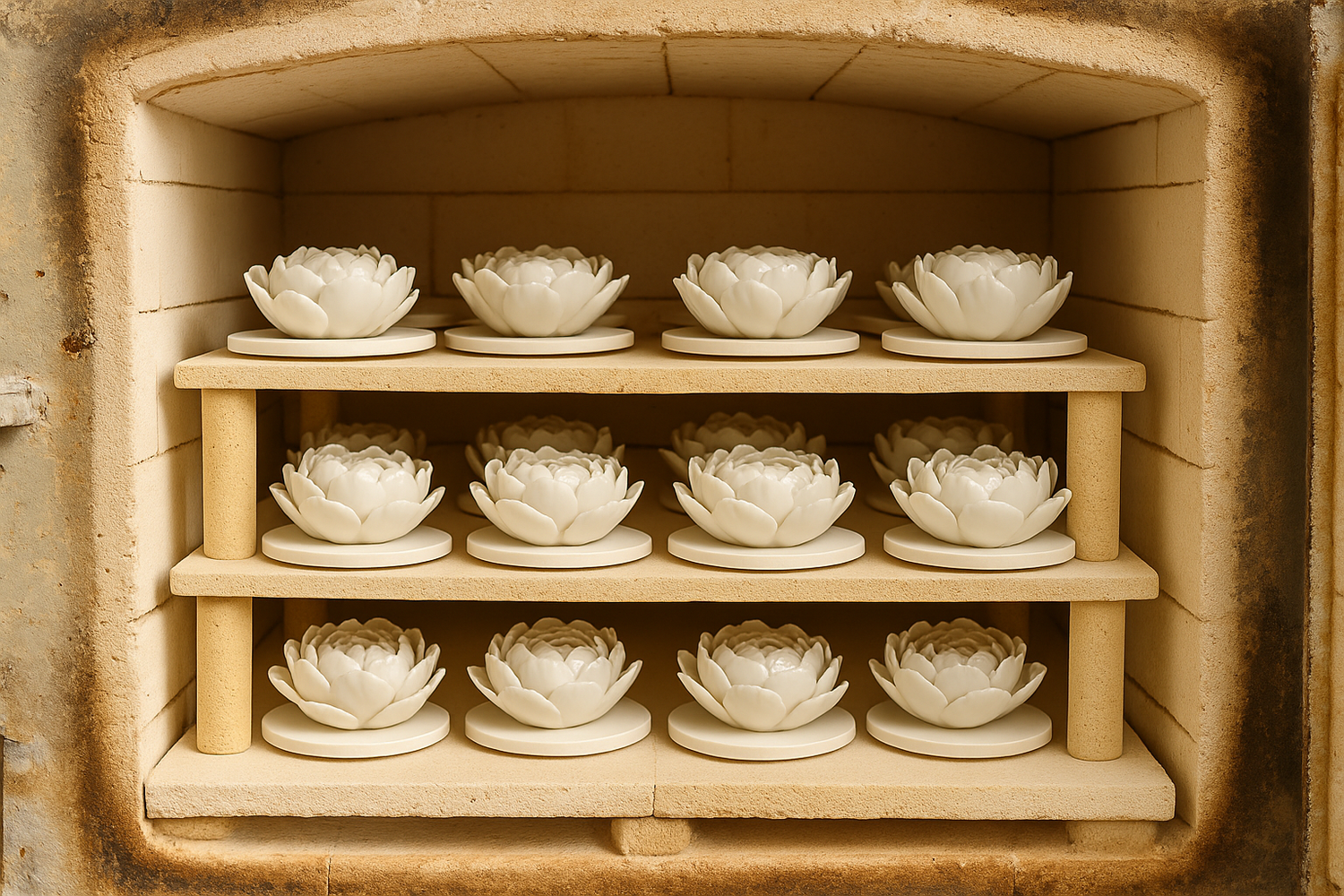
6. Kiln Loading
- Positioning:
Place on refractory shelves
→ Optimize heat distribution.
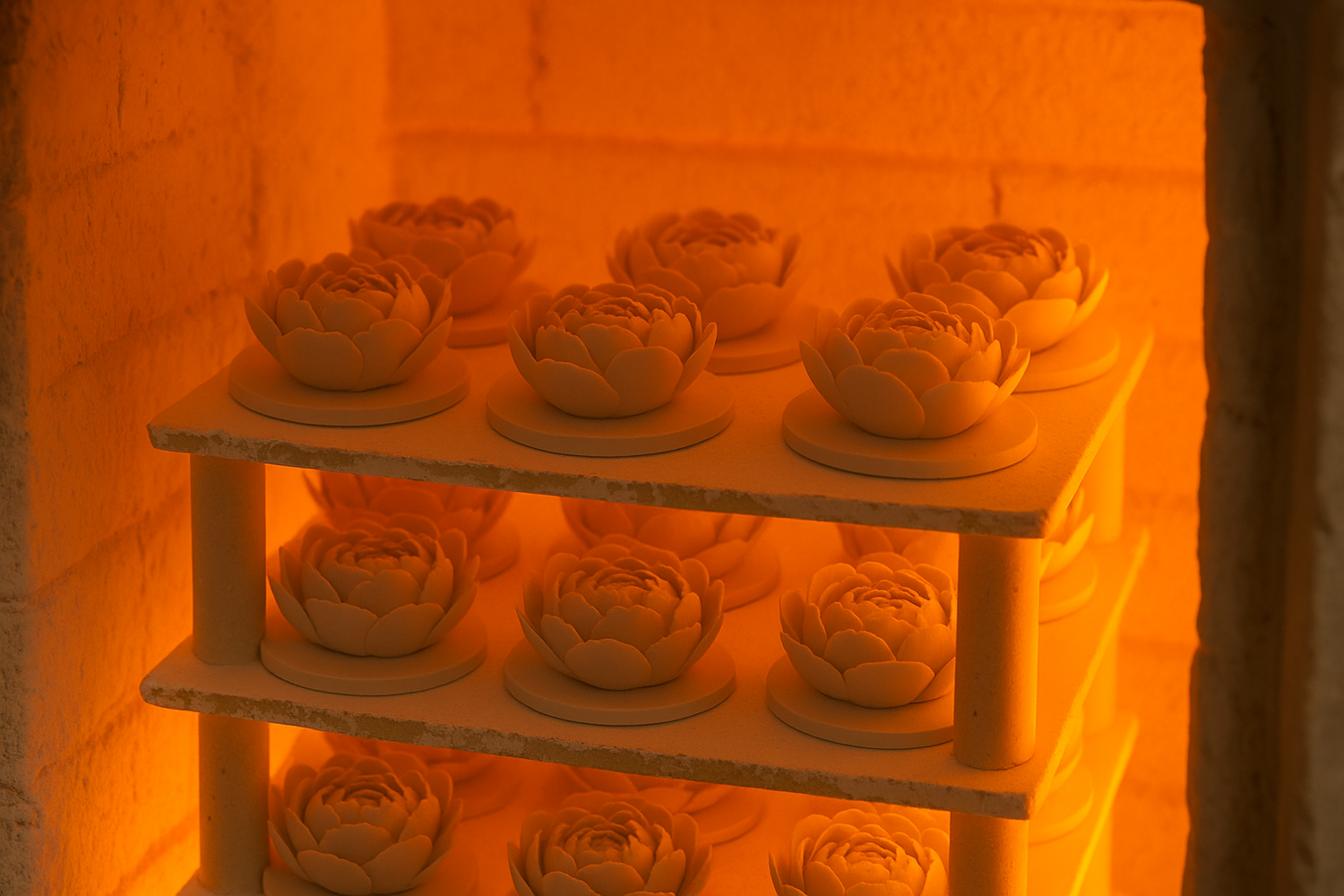
7. Firing (Critical Phase)
- Temperature Profile:
-Low temp (RT~400°C): Slow heating for dehydration.
- Mid temp (400~900°C): Controlled ramp to prevent cracks.
- High temp (1280~1400°C): Fuel-rich oxygen-deficient combustion → CO removes iron impurities → Creates "Ivory White" hue.
- Soaking: Sustain heat for vitrification.
- Cooling: Slow cooling through 800~500°C quartz inversion zone (prevents shivering).
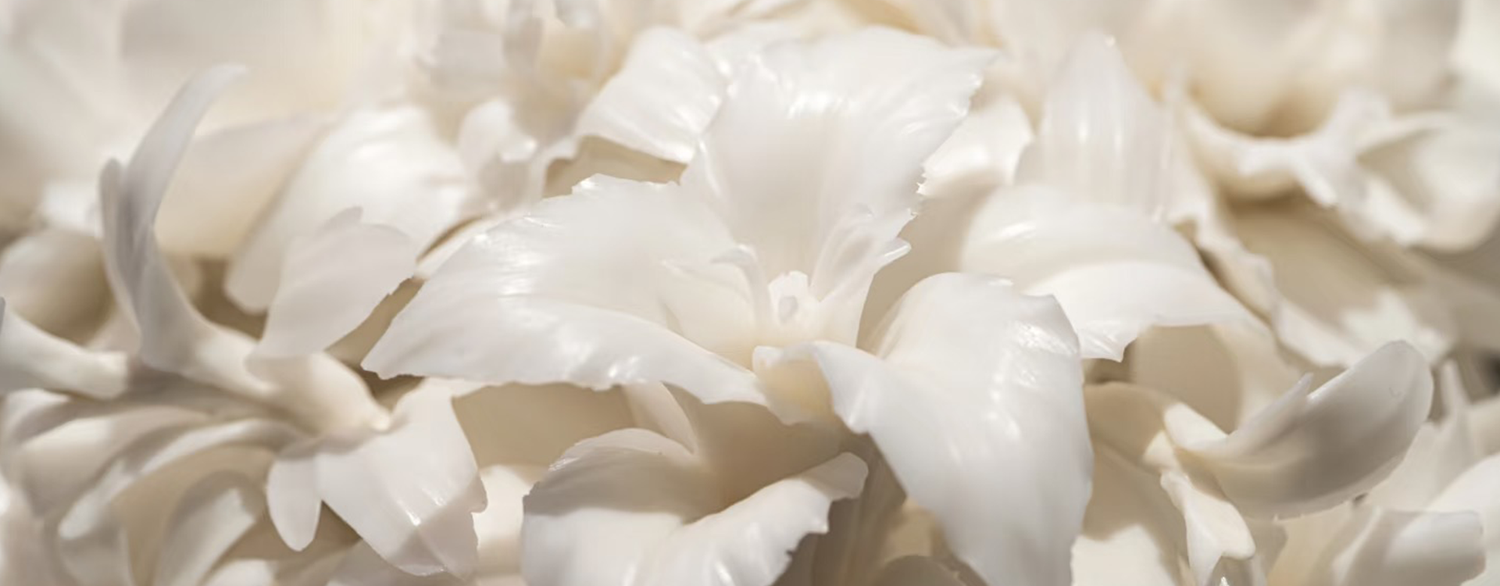
8.Unloading & Inspection
- Unloading:
Extract after full cooling (>24 hrs).
- Criteria:
- Integrity (no cracks/collapse) → Glaze (even, jade-like) → Form (no warping) → Whiteness/Translucency.
- Yield:
<20% for high-end pieces.
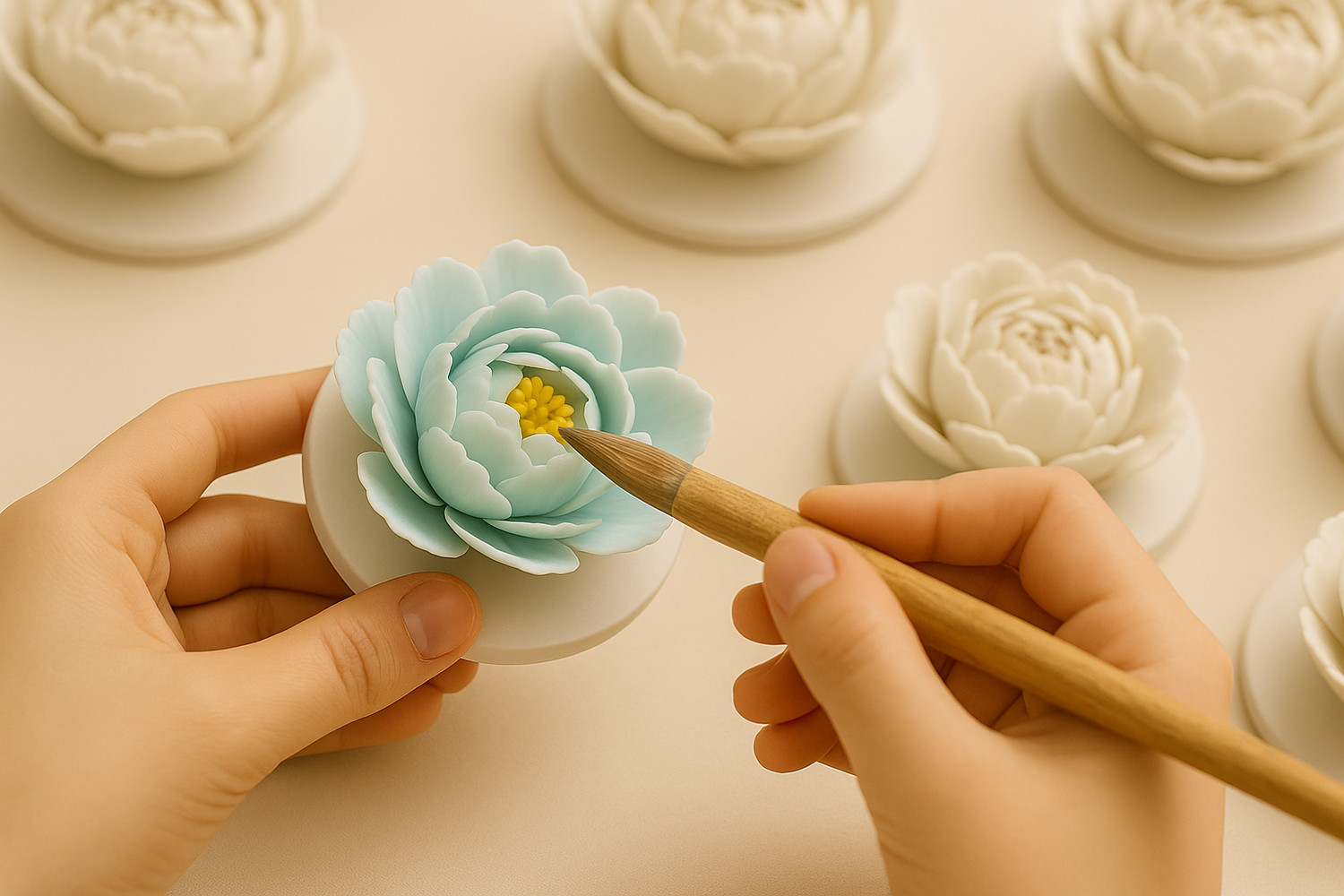
9. Finishing (Optional)
- Overglaze Painting:
Paint stamens → Refire at 700~800°C.
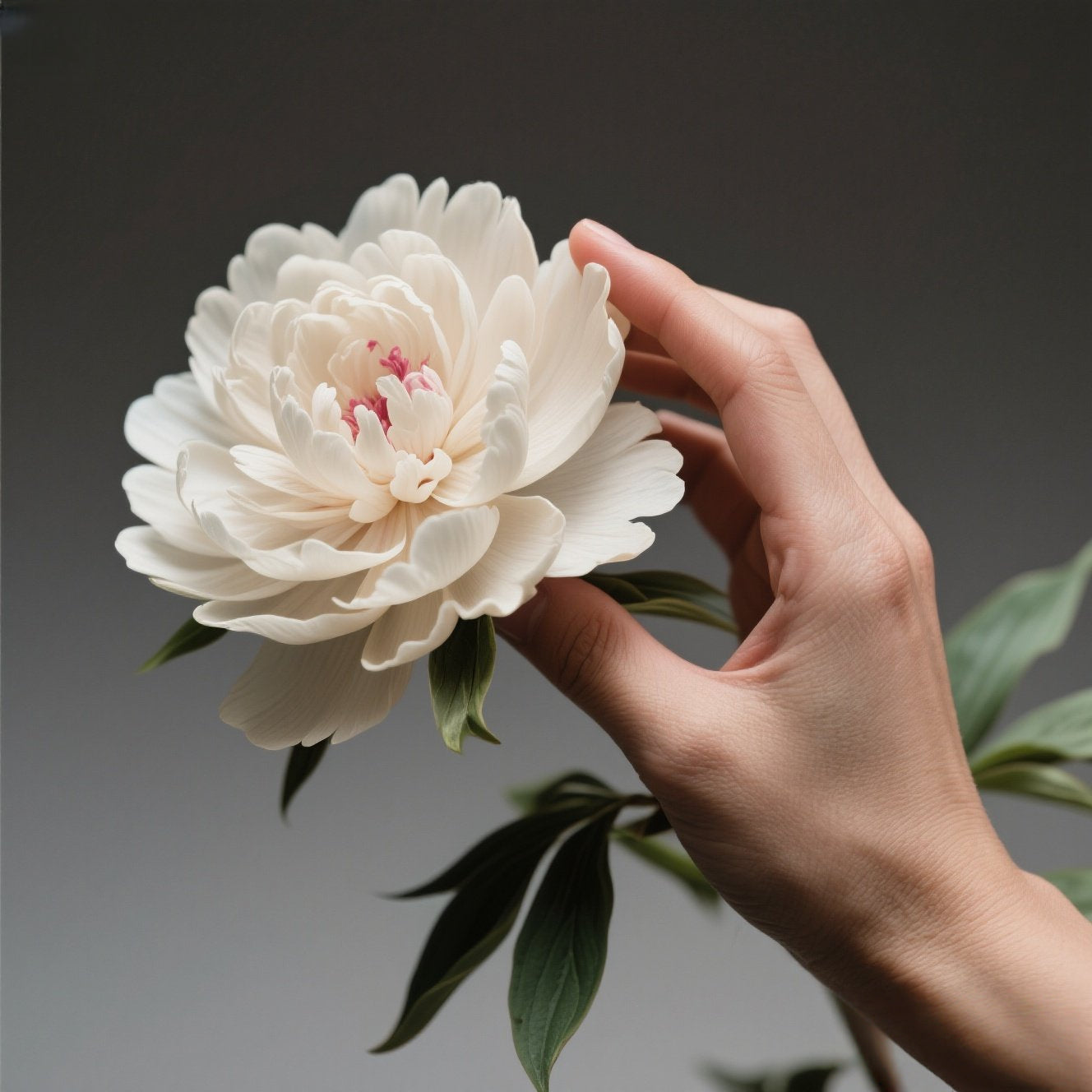
Not a living bloom, yet one that never fades.
Core Craftsmanship
- Thin: Petal thinness (01.~0.3mm).
- Precision: Microscopic texture carving.
- Ingenuity: Structural balance in assembly.
- Purity: "China Colors" from reduction firing.
- Stability: Precise drying/firing control.
Collections
-
🌹 Amour Series – For Lovers
Meaningful florals that speak from the heart.Roses, peonies, camellias and other romantic...
-
🌼 Kindred Series – For Friends
A cheerful gift to brighten someone’s day.Sunflowers, daisies, hydrangeas and zinnias —...
-
🌸 Grace Series – For Family
A gentle tribute to love that lasts.Lilies, carnations, violets and gardenias —...
-
🌿 Esteem Series – For Colleagues
Refined simplicity with thoughtful charm.Orchids, magnolias, calla lilies and chrysanthemums — calm,...
-
Water-soluble essential oil
This water-soluble fragrance essential oil utilizes advanced micro-emulsification technology to transform natural botanical extracts...